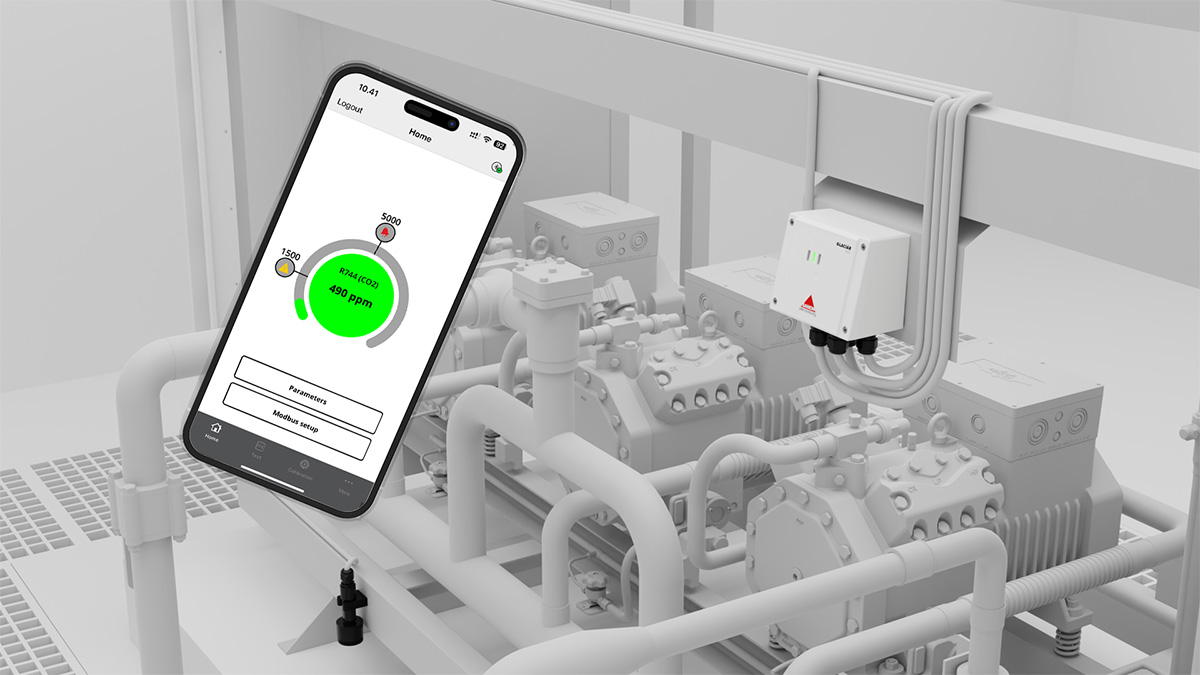
The Importance of Calibrating Refrigerant Gas Detectors
Ensuring the accuracy and reliability of refrigerant gas detectors through calibration is vitally important, because they are designed for detection of potentially hazardous gases across a diverse range of environments. Most gas detection manufacturers advise testing and calibration every 12 months as a minimum, though the frequency may need adjustment if the application is high risk, or the installation environment is especially harsh.
Imany refrigeration standards demand maintenance on an annual basis (or more frequently) in order to maintain compliance. Examples include EN 378 in Europe and ASHRAE 15 in the United States. Such maintenance is also demanded by regulations targeted at reduction of climate impact from greenhouse gas emissions, such as the F-Gas Regulation. It’s also advisable to ensure maintenance routines comply with any specific local regulations.
Advancements in Simplifying Gas Detection Maintenance
Fortunately, calibrating modern gas detectors can be a quick and intuitive process, taking only a few minutes to complete and required no special training.
In the past, calibration processes have involved manual adjustments to circuit boards, which can be prone to errors. Opting for a system where calibration gas data and calibration adjustments are made electronically ensures user-friendly calibration without room for manual errors. Utilizing a mobile app with a wizard to guide the process further simplifies things. Additionally, some manufacturers now offer plug-and-play pre-calibrated sensor modules for effortless field exchange, eliminating the need for on-site calibration and saving considerable time.
The Difference Between Calibration and Bump Test
It is important to differentiate between calibration of a refrigerant gas detector and a bump test. Whilst both can be useful, there are distinct differences.
The key point to note is that a bump test does not replace a calibration. A bump test simply exposes the gas detector to gas for a short time in order to trigger an alarm response. This is good for checking the function of alarm outputs and connected systems and gives confidence in the basic function of the instrument. However, it does not check accuracy nor make any adjustments for possible drift. Essentially, it is an unquantified test.
By comparison, a calibration exposes the refrigerant sensor to a known concentration of gas for a specified time, checks the response, and makes any necessary adjustments to the output to ensure accurate readings and a quantified, validated output. Records of calibration can and should be made to provide an audit trail for the safety system of which the gas detector forms a part.
The Importance of Calibration and Maintenance
Calibrating a gas detector is the only way to validate the performance of a refrigerant leak detection system in a quantified, auditable way. This helps to deliver:
- Compliance with industry standards.
- Safety for people working in and around the areas where potentially hazardous gas leaks could occur.
- Reliability of the refrigerant gas detection system by validating performance and adjusting for sensor drift and/or degradation over time.
- Confidence and peace of mind for users of the system and those reliant on its function for their safety.
Effective maintenance practices play a crucial role in prolonging the lifespan of refrigerant gas detectors and preserving their functionality. Regular maintenance tasks such as cleaning, inspection, and any necessary component replacement are essential to prevent potential issues and ensure the longevity of the equipment. Additionally, adhering to manufacturer guidelines for proper usage and handling can significantly impact the device’s performance and accuracy over time.
Moreover, incorporating regular checks into the maintenance routine is essential for proactive identification of any deviations or anomalies in the detector’s performance. These checks serve as early warning signs, allowing for timely intervention and corrective measures to maintain optimal accuracy and reliability.
By adopting a comprehensive approach that encompasses calibration, maintenance, usage, and regular checks, businesses can ensure that their refrigerant gas detection systems operate at peak efficiency, providing reliable protection against the potential hazards posed by refrigerant leaks. This proactive approach not only enhances safety in the workplace but also minimizes downtime and associated costs by pre-emptively addressing issues before they escalate.