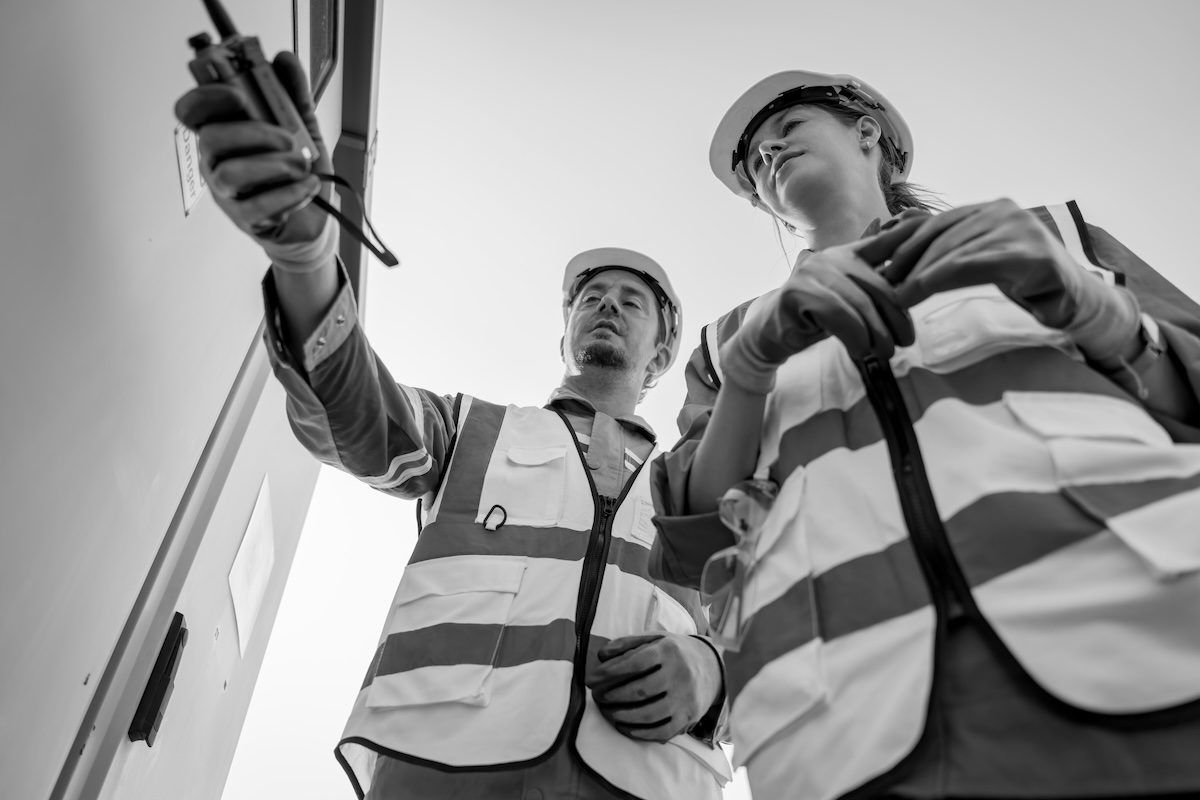
Myth-Busting Refrigerant Gas Detector Maintenance
Unfortunately, the refrigeration industry is like many other where gas detection is required, in that it faces a number of potentially dangerous misconceptions that undermine the importance of adhering to manufacturers standard maintenance recommendations and guidelines. These are not mere ploys to promote calibration gas sales, but an essential part of ensuring the performance of a refrigerant leak detection system over the course of its lifetime.
Several myths surrounding gas calibration contribute to confusion and misunderstanding; we are here to bust those myths.
- Calibration is no different from a bump test.
They are very different things. A bump test provides an unquantified validation of gas detector response, alarm functionality, and connectivity to other elements of the safety system connected to the gas detector. Calibration exposes the refrigerant sensor to a known concentration of the target gas and makes any necessary adjustments to ensure accuracy and reliability.
- Calibration is the same as adjustment.
Not true. Some sensors are extremely stable, and in the process of calibration may be proven to be within acceptable tolerances. In these instances, no adjustment is needed but the validation of calibration is still secured.
- Calibration is not necessary.
False. Many refrigerant sensor technologies will inherently drift over time. This can be as a result of component ageing, exposure to gas, or environmental conditions. Calibration brings the accuracy of the sensor back into the optimal tolerances and thereby extends the functional life of the sensor.
For sensor technologies which claim to require no calibration, it should be noted that they are not supposed to drift – but without undergoing a calibration procedure, there is no validation that they have not. Nor does it meet industry standards if no calibration check is performed.
- Calibration guarantees accuracy for 12 months.
The unfortunate truth is that calibration data is only true at the time of calibration. A multitude of things could happen to a refrigerant gas sensor in the interval between maintenance procedures, include damage (physical or environmental), a poisoned sensor, or simply drift. This is why calibration and maintenance intervals should not be set for an arbitrary 12 months. Rather they should be set with respect to the risk level of the application, the sensor type, the environment, and the manufacturers guidelines.
- Any calibration gas can be used.
Most manufacturers will recommend what calibration gas, or gases, should be used with a particular refrigerant gas detector or sensor. Important factors can include the concentration of the gas being appropriate for calibrating the range of the instrument, whether humidified gas should be used, and whether a specific grade or mixture of gas is required. In some instances, it can be critical whether the target calibration gas is mixed with air or with an inert gas such as nitrogen; this affects the basic function and operating principle of some types of refrigerant sensor. Always follow the manufacturers recommendations.
The Importance of Proper Maintenance Procedures
Understanding, acknowledging, and busting these myths is important as it underscores the significance of maintaining consistent, precise, and thorough calibration procedures for refrigerant gas detectors. Calibration serves as a cornerstone in ensuring the accuracy and reliability of these vital safety devices. However, it’s imperative to recognize that calibration alone is not sufficient. Instead, it must be accompanied by a holistic approach to maintenance, usage, and regular checks to guarantee optimal performance.