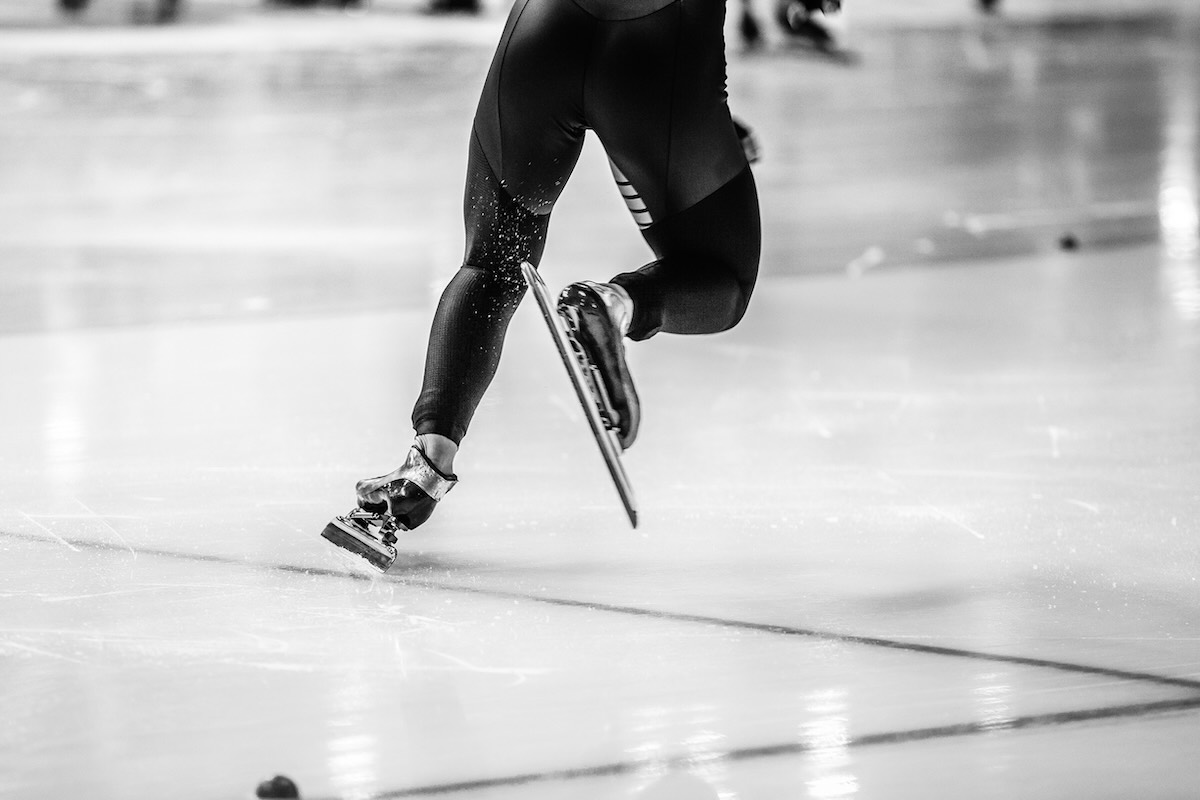
Applying NH3 Refrigerant Leak Detection
Ammonia (NH3) is commonly used in larger, industrial refrigeration applications, and often when very low temperatures need to be achieved. Typical applications include:
- Cold storage – Frozen food processing – Ice factories – Ice rinks & stadiums
Why are NH3 detectors needed?
NH3 is both lethally toxic and explosive. It is corrosive to the skin, eyes, and lungs. At high levels, NH3 is explosive.
Standards and regulations vary by country, but typical levels are as below.
NH3 concentration in air | Effects |
25ppm | Long term exposure limit – 8 hours TWA |
35-50ppm | Short-term exposure limit – 15 minutes, some physical discomfort |
70-300ppm | Severe irritation of nose, throat, and airways, risk of fluid accumulation in the lungs |
300ppm | IDLH limit (Immediate Danger to Life & Health) |
5,000ppm | Rapid respiratory arrest |
15-28% | Flammable, explosive |
Any leakage of ammonia is generally used to trigger an emergency alarm due to its acute toxicity. Although humans can detect ammonia by smell, typically in ranges from 5ppm – 50ppm, this is not a reliable method because repeated exposure can reduce sensitivity. The use of electronic gas detectors is therefore both recommended and mandated in most applications.
How to apply NH3 detection?
NH3 is lighter than air, meaning it will rise to the highest point in the room in which it leaks. Gas detectors should be installed at a high level, circa 20cm below the ceiling. Consideration should be given to the accessibility of the installation for service and maintenance.
Common practice is to install refrigerant leak detectors above the likely source of a leak, for example valves, flanges, joints, and pressure reducers. Detectors can also be installed above areas with a high concentration of refrigerant, such as compressors, storage tanks/cylinders, pipes, and conduits.
Consideration should be given to air flow and ventilation, both natural and mechanical. It typically takes a long time for leaked gas to evenly disperse into the environment, so clouds of leaked gas can be moved by ventilation. Placing refrigerant gas detectors in this air flow is good practice for effective detection.
NOTE: There is no general rule or standard for establishing the appropriate number of sensors and their location for each application. Therefore, the guidance given is intended as support for installers, and not as rules in their own right. All local, state, and national regulations should be adhered to.
NH3 Gas Detector Selection
NH3 is typically detected using electrochemical sensors. This technology has a number of benefits in refrigeration applications. These include high selectivity, minimal cross-interference, and high stability. The sensors are also highly accurate and can be ranged for the required target measurement concentration.
Electrochemical sensors have a limited life span, typically requiring replacement every 2 years. There are, however, some refrigerant gas detectors now on the market with field proven NH3 sensors with a lifetime in excess of five years.
Selecting a refrigerant gas detector with simple maintenance procedures is particularly important due to the periodic requirement for replacing the sensor, and the more frequent requirement (at least every 12 months) to test and calibrate the instrument.
Applications for NH3 detection often require detection in high-pressure vent lines from pressure relief valves. Special mounting accessories should be used in this case, in order to ensure effective measurement and to protect the gas detector from damage by over-pressurisation.
A suitable NH3 refrigerant leak detector should have the following characteristics:
- Fast response time
- Appropriate temperature range (e.g. -30°C – +50°C)
- Suitable IP rating for the installation environment (e.g. IP66 or IP67)
- outputs for system integration, control & safety alerts (e.g. relays, Modbus, analog outputs)
For any areas zoned as being potentially explosive, a detector with the appropriate EX-certification for that zone should be selected.